Locations & Technology - Capacity Optimisation on Limited Storage Space
Burkhardt Fruchtsäfte, a company with a 90-year tradition, produces around 25 million bottles annually for customers within a 250 kilometer radius. Offering over 80 products, Burkhardt supplies premium juices to both the hospitality industry and retailers.
With increasing filling volumes and an expanding product range, the company needed more storage capacity at its Machtolsheim headquarters. However, this had to be achieved without major construction work. In collaboration with Schulte Berater + Partner, the entire warehouse layout was redesigned, and the logistics processes were reorganized using modern storage technologies.
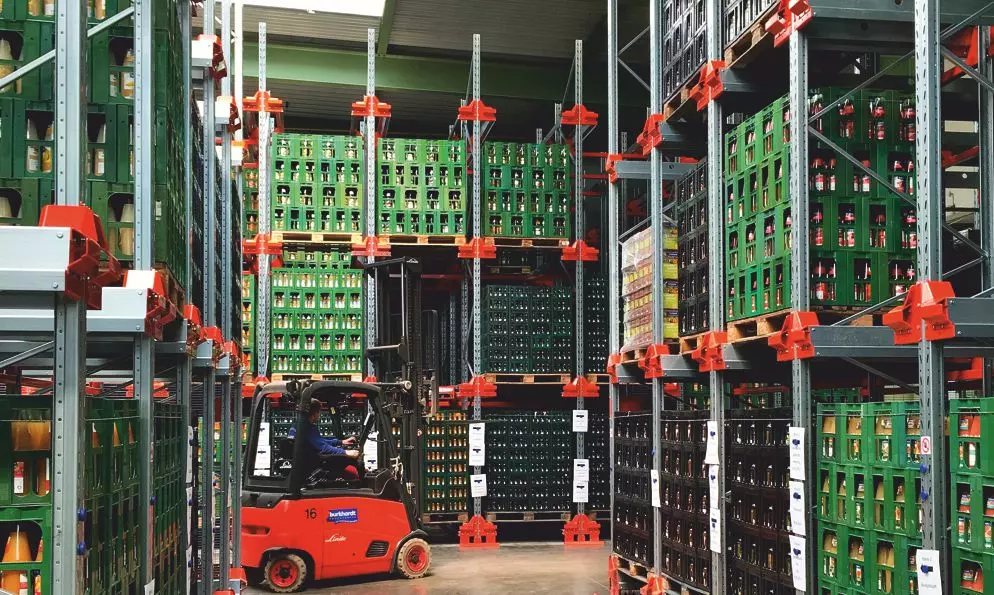
Challenge - Warehouse capacity expansion & production space optimization
The expansion of the bottling lines required additional space, but there were no free areas available within the production facility, and building extensions were not an option. A portion of the existing finished goods warehouse had to be repurposed for the new bottling line, creating a capacity bottleneck. This issue was made worse by the increasing need for storage space. Using an existing external warehouse would have required a costly and time-consuming shuttle system, so the ideal solution was to increase storage capacity within the current building footprint.
Solution - Conversion, separation, reduction, repositioning, and compensation
A detailed analysis of the product range and inventory situation led to a plan that increased capacity and improved internal processes without requiring expensive construction. Key actions included,
- Switching storage systems: Replacing block storage with compact and flexible technology using shuttle-operated channel storage
- Reducing traffic routes: Introducing space-saving reach trucks to minimize transport paths
- Compensating for complex shuttle handling: Improving processes in other warehouse areas to balance the added complexity in the shuttle-operated storage
- Separating picking and storage processes: Establishing a dedicated picking zone, eliminating the need for picking in the block or rack storage areas
- Repositioning top-selling items: Moving the most popular products closer to production and loading areas for quicker access
Result - The reorganization of the finished goods warehouse and its processes delivered:
- an almost 10% increase in capacity despite losing storage space
- more productive warehouse operations with a reduced error rate
- A significantly improved utilization of the finished goods warehouse
- seamless implementation of the new bottling line in production
Contact Person - Would you like more information or do you have a similar project?
I look forward to hearing from you.
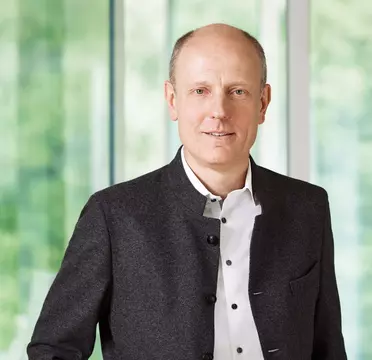