Locations - Davert GmbH Expands its Production Capacity and Gets a Fully Automated High-Bay Warehouse
Davert GmbH, a specialist in organic food with over 30 years of experience insourcing and processing raw materials from certified organic farming, was rebranded to Midsona Deutschland GmbH after its acquisition by Swedish Midsona AB in May 2018. Davert’s clients include both organic food retailers and well-established grocery stores.
In 2014, Davert opened a new site in Ascheberg with the support of Schulte Berater + Planer. Following an initial warehouse expansion in 2016, the company needed to further increase its capacity to accommodate growing demands for production and logistics.
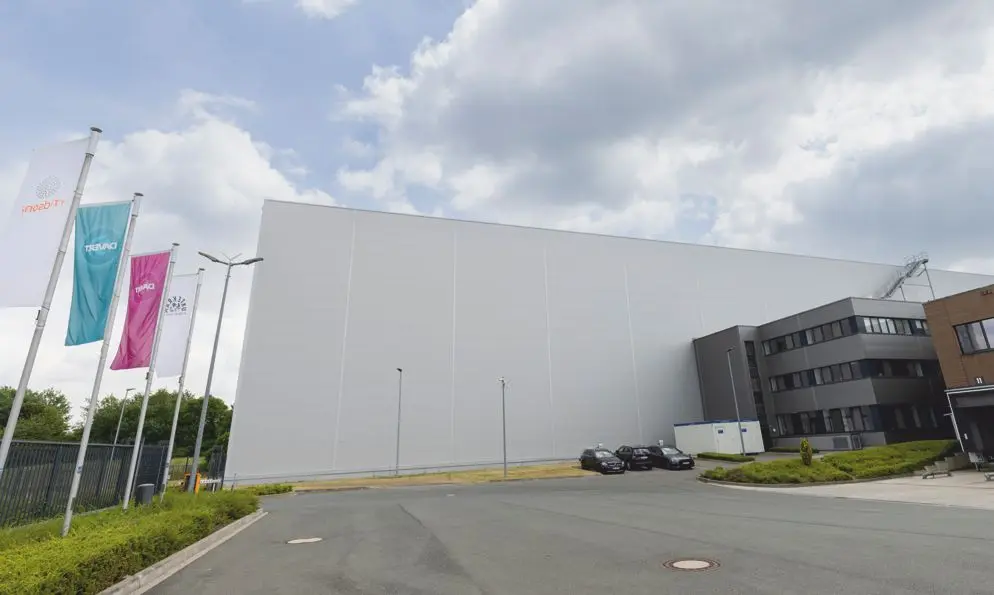
Challenge - Warehouse capacity and production space optimization
The goal was to expand the warehouse capacity by at least 50%, with potential for further expansion. Additionally, production space was required for new filling machines to handle new product categories. The site concept, based on a 2012 master plan developed with Schulte Berater + Planer,was designed to integrate the new material and product flows while maintaining optimal internal processes. To implement the new processes, automation solutions and software/hardware interfaces had to be defined. Moreover, partners for high-bay storage, automated guided vehicles (AGVs), roofing, and fire protection systems had to be selected and coordinated.
Solution - Redesign, integration, expansion, and automation
The project involved rethinking and expanding the facility while automating key processes. Specific steps included
- new warehouse design: A silo-style high-bay warehouse, detached from the main building, was developed. The connection to the main building was established via a continuous conveyor in a pallet tunnel
- Expansion of production space: An intermediate structure between the main building and the high-bay warehouse provided the required additional production area
- Automation: Automated guided vehicles (AGVs) were introduced to relieve employees from repetitive transport tasks, improving efficiency in the three-shift operation
Results - The planning, development, and commissioning of the site expansion resulted in
- the reintegration of previously outsourced raw and finished goods storage, with handling and cost advantages
- the inclusion of new product categories in the production programme, supporting sustainable growth
- a high-performance production environment and more efficient logistics processes
Contact Person - Would you like more information or do you have a similar project?
I look forward to hearing from you.
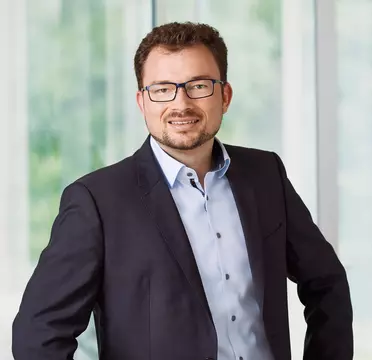